Tips & Tricks
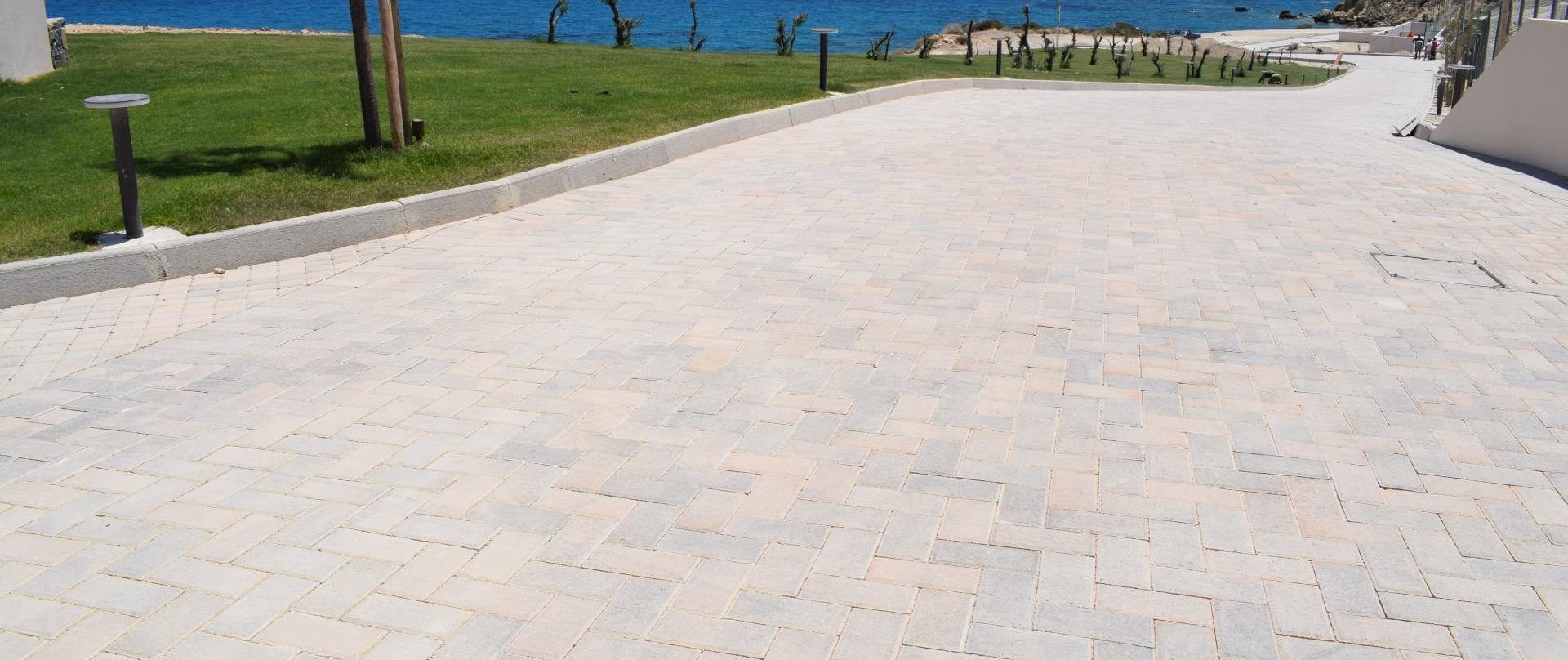
Matonela® terrazzo tiles:
Matonela® is a natural material that "lives" and "breathes" like all natural materials (marbles, natural stones, etc.). For this reason, it needs care and attention both during and after installation. Protect it as much as possible during and after installation.
To prevent stains during installation caused by other works that may be carried out in the building (e.g. oily paints) and by carelessness (e.g. coffee, milk, etc.), cover the floor with a nylon or other protective material once it has been laid.
Immediately after installation and before trimming, and after the floor has been completely cleaned of foreign bodies (dust) and mopped (with a neutral cleaner for marble, or with water if completely clean), waterproof Matonela® tiles terrazzo with a recommended impregnating sealer for future protection.
Installation of Matonela® tiles without joints in order to imitate a poured terrazzo floor:
The dimensions of Matonela® tiles are precise, with minimal tolerances and almost zero contractions – expansions. Thus, installation without joints is indicated, as long as you remember to leave expansion joints every 10 meters.
Poured concrete floor or precast concrete paving block floor?
In most regions of the world the cost for a 10 m2 floor of concrete paving blocks is half the cost of building a concrete floor. The larger the project, the more the cost of pouring concrete is reduced.
Nevertheless, precast concrete paving blocks offer a much greater variety of designs and colors. Also, their strength is much higher, almost double, than conventional concrete. In addition, replacing a broken block is much easier than repairing a cracked or broken concrete walkway.
The role of spacer nibs in concrete paving blocks:
Spacer nibs allow for the automatic creation of joints among the paving blocks. Thus, it becomes possible to fill in the gaps with grouting sand. Without the existence of the joint, the blocks would be installed in touch with each other causing the edges to shatter and chip-off when dynamic loads are applied (e.g. car traffic).
Advantages of the technology of double layer blocks:
The benefits of utilizing the double-layer technology in the manufacture of concrete paving blocks are substantial. The incorporation of a second layer in offers significant perks:
1. The base mix utilizes coarse-aggregate concrete, thereby attaining high tensile splitting strength levels.
2. The surface mix incorporates fine-grain concrete, resulting in an enhanced finish and superior abrasion resistance
3. The surface longevity is assured, given the increased use of high-strength cement (specifically, Portland type CEM 52.5N) in this layer
4. It opens up the potential to manufacture paving blocks that meet specific needs such as CoolPave® blocks with reflective qualities, EcoActive® blocks with photocatalytic capabilities, permeable EcoDrain® blocks, paving blocks resistant to abrasion and chemicals, among others.
Without the second layer technology, producing such blocks would be practically unfeasible due to the need for high-cost, specialized raw materials. Including these materials into the entire mass of the blocks (measuring 6 cm thick or more) rather than just into the thin surface layer (of 0.5 cm thickness), is not economically viable (with a cost ratio of at least 12 times higher). Moreover, using these materials throughout the block's mass would hinder the achievement of necessary technical attributes. For instance, blocks incorporating cool materials throughout their mass need to maintain a sufficiently sleek surface to meet the required reflectivity values. This would compromise the essential tensile splitting strength.
Moreover, this is also confirmed by the abrasion resistance tests we carry out in our laboratory which give (for the double-layer blocks) abrasion resistance results of < 23 mm! This translates to a surface "eating" depth of less than 0.66mm!
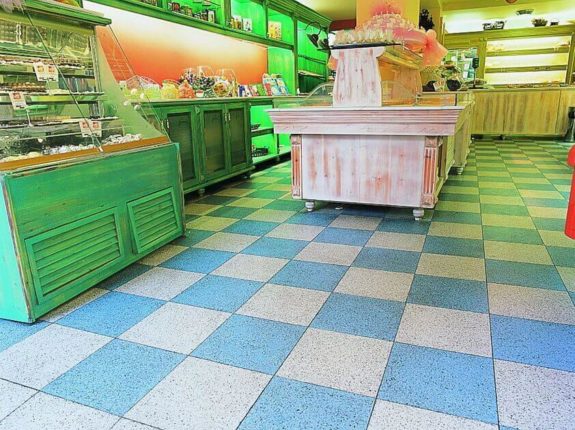
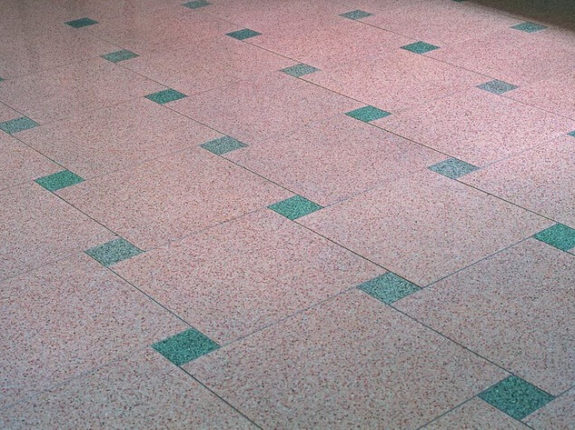